SECONDARY BATTERY
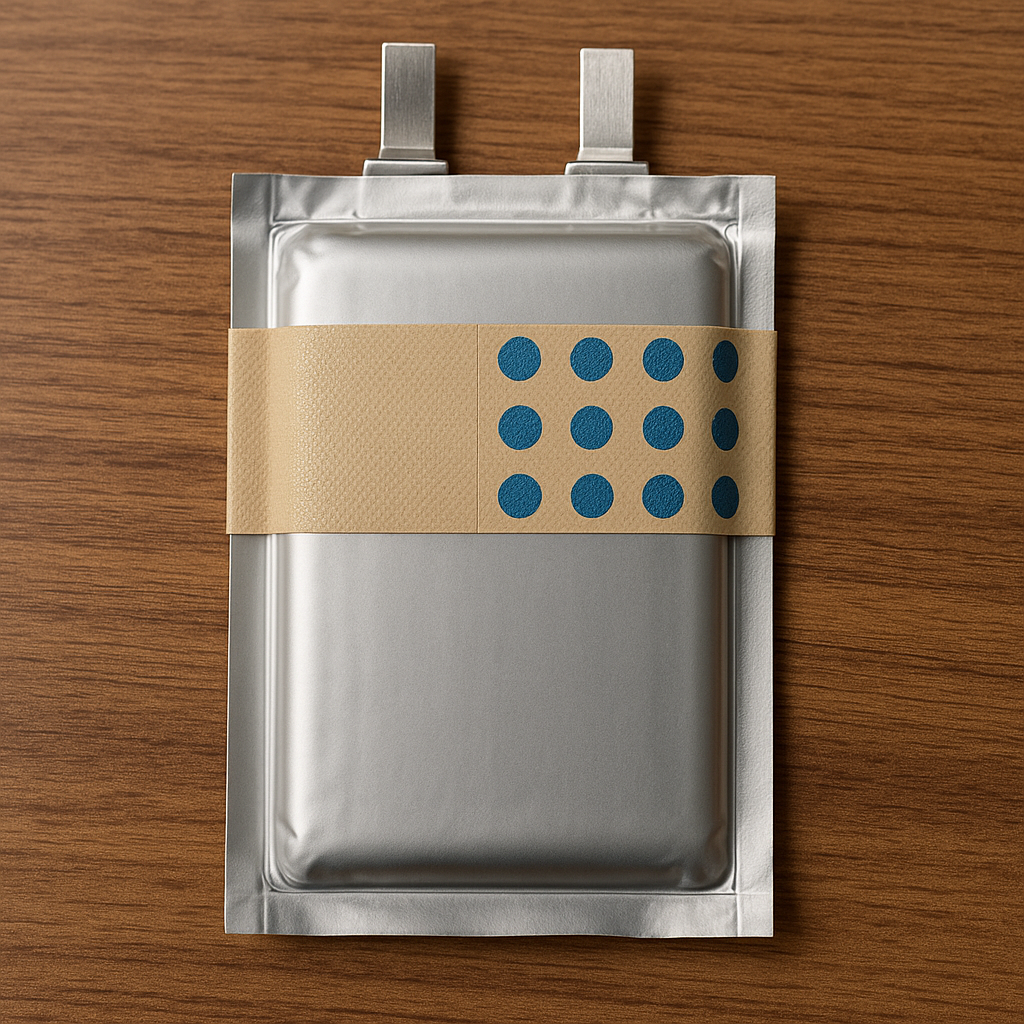
Invented by BAEK; Moo Ryong
Unlocking the secrets behind battery inventions can seem tough, but sometimes, the best ideas are easy to grasp. Today, let’s explore a new secondary battery design based on a recent patent application. We’ll break it down so anyone can learn about the need for this battery, how it’s different, and what makes it special. By the end, you’ll see how a small change in something as simple as tape can make a big difference in technology.
Background and Market Context
Batteries make our world work. From phones and laptops to electric cars and tools, they are everywhere. In recent years, the demand for rechargeable batteries, also called secondary batteries, has exploded. This is because people want devices that last longer, are safer, and work better. As more gadgets and cars run on batteries, there is a race to create batteries that are not only powerful but also safe and reliable.
Most of the batteries in your phone, laptop, or electric car are rechargeable. These are different from the batteries you use once and throw away. When people talk about “secondary batteries,” they mean batteries you can use again and again by charging them. This is important for the planet and for people who want to save money.
Today, battery makers face several big problems. As batteries get smaller and more powerful, they become harder to make safely. A battery needs to be sealed tightly so nothing leaks out, and so no dirt gets in. If a battery seal is weak, it can mean trouble: short circuits, leaks, or even fires. In addition, batteries are put into all kinds of devices in all kinds of places, so they need to be tough and resist damage.
One part of the battery that keeps it safe is a pouch that wraps around the battery’s power cells. This pouch needs to be covered and protected. Usually, companies use special tape with glue on the inside to keep the pouch sealed and secure. But tape isn’t perfect. If the glue leaks or gets exposed, it can cause sticky messes, attract dirt, or even damage the device the battery is inside. Small problems like exposed glue can turn into big headaches for manufacturers and users.
As more companies try to make batteries faster and cheaper, these small problems become even more important. A battery that is hard to make or has quality issues can slow down production and create costly recalls. So, even something as simple as the way a tape is used on a battery can be a big deal in the world of battery production.
That’s why inventors are looking for new ways to seal batteries better, make them safer, and avoid sticky messes. The new patent we’re exploring today aims to solve these real-world problems with a smarter, safer battery tape design.
Scientific Rationale and Prior Art
To understand why this new battery idea matters, let’s look at how battery pouches and tapes have worked up until now, and why they can be a problem.
Inside every rechargeable battery is something called an “electrode assembly.” This is where the battery stores and releases energy. To keep this assembly safe, it is put inside a pouch. The pouch acts like a strong bag, keeping everything inside and protecting it from water, dust, and other dangers. The pouch is usually sealed at the edges by melting the material together, a bit like sealing a plastic sandwich bag.
But pouches alone aren’t enough. To make sure the pouch doesn’t open or move, manufacturers use tape with glue on it. This tape is wrapped around parts of the pouch and pressed down to hold everything tight. The tape also adds an extra layer of insulation so the battery doesn’t short out or get damaged if it bumps into something.
In the past, most tapes used on batteries had glue all over one side, with the same amount of stickiness everywhere. This seems simple, but it can cause trouble. If the glue is too strong, the tape might be hard to apply, or it might rip the pouch when the battery moves or expands. If the glue is too weak, the tape might peel off, letting the pouch open. Even worse, if the glue squishes out at the edges or corners during manufacturing, it can get on the battery or inside the device. This not only looks bad but can lead to battery failures or even damage the gadget that uses the battery.
Some past inventions have tried to solve this by changing the tape material or by making the glue stronger or weaker overall. Others have made tapes with different shapes or extra layers. Some battery makers have used tapes with “dots” or “stripes” of glue instead of covering the whole tape with it. These ideas help a little, but they don’t always stop glue from leaking out during production, especially at the tape’s edges or corners.
Another problem is that batteries get hot and cold, and they can expand or shrink a little during use. If the tape isn’t flexible or if the glue is exposed, it can come loose over time. This is bad for safety and for how long the battery will last.
So, even though many smart people have worked on battery tape designs, there is still a need for a solution that keeps the tape in place, keeps the glue from leaking out, and is easy to use in factories. The new patent tackles these problems head-on by changing not just the tape’s shape, but also where the glue goes, and how sticky it is in different places.
This approach is different from earlier ideas because it combines several smart tricks: using tapes with different glue strengths in different spots, creating “finishing areas” with no glue at all at the edges, and adding thicker, dam-like edges to catch any glue that might try to escape. This helps make batteries safer, cleaner, and easier to make.
Invention Description and Key Innovations
Let’s get to the heart of the patent: what’s actually new, and why does it matter? The invention is all about a better way to use tape on a battery pouch. Here’s how it works, step by step, in plain language.
The battery in this invention has three main parts:
First, there is the “electrode assembly,” which is the part that holds and makes the electricity. Second, there is the “pouch,” which is like a strong bag that wraps around the electrode assembly to keep it safe. Third, there is the “cover tape,” which is a special tape that goes around the pouch to keep it sealed and protected.
Now, here’s where things get clever. The cover tape doesn’t just have one kind of glue on it. Instead, different parts of the tape have different strengths of glue. In some places, the glue is very strong to hold the tape in place tightly. In other spots, the glue is much weaker, just enough to keep the tape from lifting, but not so strong that it puts too much stress on the pouch or oozes out. And, at the very edges of the tape, there is no glue at all—these are called “finishing areas.”
Why is this important? When a battery is made in a factory, the tape is pressed down hard onto the pouch. If glue covers every part of the tape, some of it can squish out the sides, especially if the glue is sticky or thick. This can leave little bits of glue sticking out, which can catch dirt or cause trouble later. By making the edges of the tape free from glue (the finishing areas), even if glue tries to move, it gets stopped, like a dam stopping water.
The tape is also designed with special areas called “dot areas” and “fixing areas.” In dot areas, the glue is applied in small spots or dots, so it doesn’t cover the whole surface. This makes the glue weaker in those spots, which is good for places where you don’t want the tape to be stuck too hard. In fixing areas, the glue is much stronger to keep the tape from moving or peeling off. The base area of the tape (the part that goes under the battery) has a middle strength of glue, just enough to keep it in place but not so much that it causes problems.
Here’s a simple way to imagine it: think of the tape like a special sticker. Most stickers use the same glue everywhere. This invention uses strong glue where it’s needed most, weak glue where it’s not, and no glue at all at the very edge. The result is a battery that’s safer, easier to make, and less likely to have glue problems.
The patent also spells out the exact strength of the glue in different areas. The base area has glue that holds with a force between 0.20 to 0.50 kilograms per 25 mm. The dot areas use even weaker glue, between 0.05 to 0.25 kilograms per 25 mm. The fixing areas use much stronger glue, between 1.10 to 1.40 kilograms per 25 mm. These numbers are important because they help factories use the right glue in the right place, making the battery safer and easier to build.
Another smart part of the invention is the “finishing area” at the tape’s edge. This part has no glue at all, and it can even be made thicker than the rest of the tape, like a tiny wall. If any glue tries to move toward the edge during production, this thicker part stops it, keeping the edge of the battery clean and free from glue.
The way the tape is wrapped around the battery is also special. The tape goes under the battery, up the sides, and partly over the top. The dot areas cover the upper parts of the battery, where it’s more likely that glue could get exposed. By using weaker glue here, the risk of sticky messes is much lower.
In short, the invention is a smarter, safer way to tape up a battery. It uses different amounts of glue in different places, leaves the edges glue-free, and can even use thicker edges to stop glue from leaking out. This makes batteries safer, cleaner, and easier to make, which is good for everyone from battery makers to people using phones and electric cars.
Conclusion
This new battery design might seem like a small change, but it solves a big problem in a simple, clever way. By changing how tape and glue are used on battery pouches, the invention keeps batteries safe, clean, and easy to manufacture. It’s a perfect example of how sometimes, small details—like where you put glue—can make technology better for everyone. As devices get smaller and smarter, little inventions like this one help keep the world running smoothly.
Click here https://ppubs.uspto.gov/pubwebapp/ and search 20250219217.