Invention for Systems and Methods for Communicating with Motion Control Systems and Devices
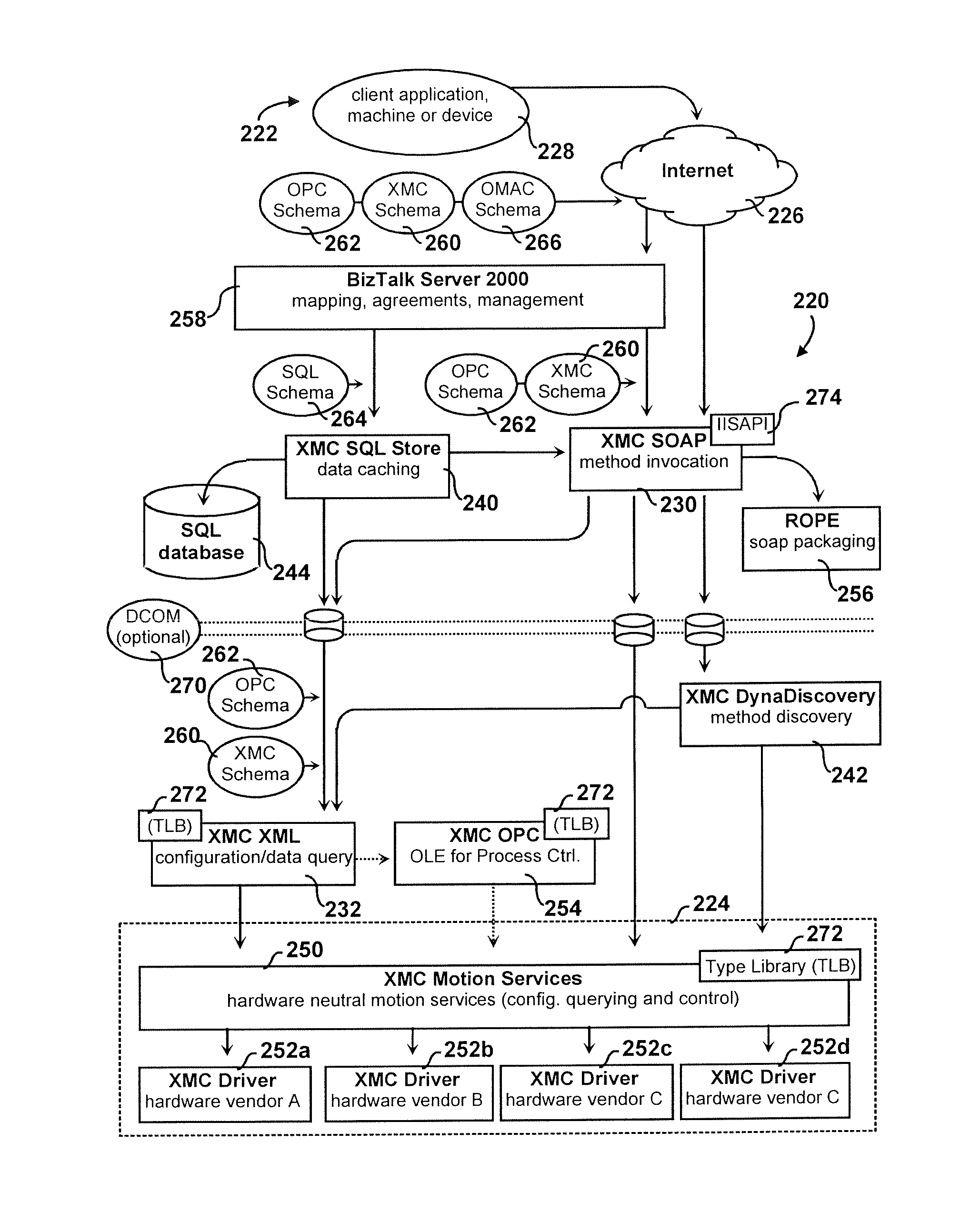
Invented by David W. Brown, Jay S. Clark, Roy G Biv Corp
Motion control systems and devices are used to control the movement of machines and equipment. These systems are essential in many industries, as they help to improve efficiency, productivity, and safety. However, to fully realize the benefits of motion control systems, it is important to have effective communication between the systems and the devices they control.
This is where systems and methods for communicating with motion control systems and devices come in. These systems and methods allow for seamless communication between the motion control systems and the devices they control. This enables operators to monitor and control the systems and devices in real-time, ensuring that they are operating at optimal levels.
One of the key drivers of the market for systems and methods for communicating with motion control systems and devices is the increasing adoption of Industry 4.0 technologies. Industry 4.0 is a term used to describe the integration of advanced technologies, such as the Internet of Things (IoT), artificial intelligence (AI), and machine learning (ML), into industrial processes.
Industry 4.0 technologies are transforming the way that industries operate, and motion control systems are no exception. By integrating these technologies into motion control systems, operators can monitor and control the systems and devices remotely, using data analytics and predictive maintenance to optimize performance.
Another driver of the market for systems and methods for communicating with motion control systems and devices is the increasing demand for automation in various industries. Automation is becoming increasingly important in industries such as manufacturing, where it is used to improve efficiency, reduce costs, and increase productivity.
To fully realize the benefits of automation, it is important to have effective communication between the motion control systems and the devices they control. Systems and methods for communicating with motion control systems and devices enable operators to monitor and control the systems and devices remotely, ensuring that they are operating at optimal levels.
In conclusion, the market for systems and methods for communicating with motion control systems and devices is growing rapidly, driven by the increasing adoption of Industry 4.0 technologies and the demand for automation in various industries. As these technologies continue to evolve, we can expect to see further growth in this market, as operators seek to optimize the performance of their motion control systems and devices.
The Roy G Biv Corp invention works as follows
A motion-control system includes a motion-control application created by a motion-control system designer, an application programming component that defines an API function and a security setting system for determining the access of the motion control app to the API function. An API function is included in a motion control application. Motion control application calls an API function to the motion component. Based on the API call, the motion control component creates a motion command. Security settings limit the generation of motion control commands by the motion component. The motion device executes the motion task in response to the motion control command.
Background for Systems and Methods for Communicating with Motion Control Systems and Devices
A motion control device’s purpose is to move an item in the desired direction. A motion control device is composed of two basic components: a controller, and a mechanical unit. The mechanical system converts signals generated by a controller into movement.
While the mechanical system is commonly composed of a drive and an electric motor, other systems such as vibrational or hydraulic systems can be used to move an object in response to a control signal. A motion control device can also include a number of motors and drives to control the movement on multiple axes.
The present invention will be discussed in more detail in relation to a mechanical system that includes at least one electrical motor and drive with a rotating shaft. This application is described here in greater detail. The principles of the invention can be applied to any mechanical system which generates movement in response to a control signal. The claims should be used to determine the scope of the invention and not the detailed description.
In a mechanical device consisting of a controller and an electric motor, the motor must be physically connected to the moving object so that the rotation of the motor shaft can translate into the movement of the object. The drive is a power amplifier that provides power to a motor in order to rotate it in a controlled way. The controller controls the drive based on the control commands so that the object moves in the desired way.
These basic components are usually placed in a larger system for a specific purpose. One controller, for example, may work in conjunction with multiple drives and motors to move a tool along an established path relative to the workpiece.
Also, the basic components described are often used with a programmable logic control (PLC) or host computer. The PLC or host computer allows the use of high-level programming languages to generate commands that are then passed to the controller. The software running on the computer host is designed to make it easier to program the controller.
Companies who manufacture motion control devices have traditionally been hardware-oriented companies, which produce software for the hardware they manufacture. These software products are sometimes referred to low-level programs. Low level programs work with motion control commands specific to each motion control device. These low-level programs give the programmer a high degree of control over the hardware. However, they are very hardware-dependent.
High-level software applications (also called factory automation programs) allow factory system designers to create application programs which combine multiple input/output devices including motion control devices into a complex automated factory environment. The factory automation applications can be used with any number of I/O device, provided that the high-level software supports them. The factory automation program does not allow custom applications developed by other software developers to use the motion control capabilities.
These programs also do not give the programmer much control over each device that is part of the system. “Each program created with a factory application must be run in the context of this application.
In this context, several individuals are involved in creating and operating motion control systems dedicated to a specific task. These individuals usually have specialized backgrounds which enable them to perform specific tasks in the overall creation of a motion-control system. There is a need for systems and techniques that allow individuals with different backgrounds to work together on motion control systems.
Motion control systems are used to perform repetitive and well-defined tasks in industrial settings, such as welding, part assembly, etc. Motion control systems are also used in non-industrial environments in the form toys, appliances and the like.
Motion control data defines the specific motion task that a motion control system will perform. Motion control data are a set instructions that were traditionally written in a software language dependent on hardware. However, systems and methods exist to create hardware independent motion data. The term “application program” will be used in the discussion below. The term ‘application program’ will be used in the following discussion to refer to an individual set of motion data. The terms “application programmer” The terms?application programmer? or?programmer’ will be used to refer to the person who writes the application program.” “The person who wrote the application program
Motion control systems use a motion controller that converts motion control data to physical movements. The motion control device may be connected to a computer which stores the application programs, and then transfers them to the device. The system operator is the term used to describe the person who is responsible for the motion control device.
In both industrial and nonindustrial settings, the application program is often written at one location by an application programmer and then executed on a motion-control system at another location. In some cases, an application program can be transferred over a communication network like the Internet from the source location to the destination.
From the perspective of an application programmer the details of the system of motion control can either be known or unknown. The application programmer might also not be aware of the specifics of the communication network that is used to transfer the motion control data.
One scenario that is particularly relevant to the invention is when an application programmer creates an application program to perform a motion task, but does not have the knowledge or wants to not be restricted to a specific motion control system. The details of a software platform or motion control device may not be known to the programmer or the operator of the system may want to have flexibility in changing one or both.
The need for systems and techniques that allow the transmission of motion data from a source over a communication network to a motion system is also present. This invention is particularly important when the application programmers do not know the specifics of the motion-control system.
The present invention has a special importance when it comes to a motion-control system that uses multiple programming languages or language variants. As we have discussed, motion control device manufacturers are typically hardware-oriented companies who produce low-level software dedicated to their hardware. Low-level programs are usually designed to work with motion control commands specific to the device. These low-level programming languages give the programmer a high degree of control over the hardware. However, they are very hardware dependent.
High-level software applications (also called factory automation programs) allow factory system designers to create application programs which combine multiple input/output devices including motion control devices into a complex automated factory environment. The factory automation applications can be used with any number of I/O device, provided that the high-level software supports them. The factory automation program does not allow custom applications developed by other software developers to use the motion control capabilities.
These programs also do not give the programmer much control over each device that is part of the system. “Each program created with a factory application must be run in the context of this application.
The present invention can also be applied in a more specific environment, where a general movement device is used to implement a program that was written for a CNC. The present invention is applicable to all motion control devices that are able to generate movement in response an application program.
Click here to view the patent on Google Patents.