Invention for Methods to Fabricate Three-Dimensional Print Composites
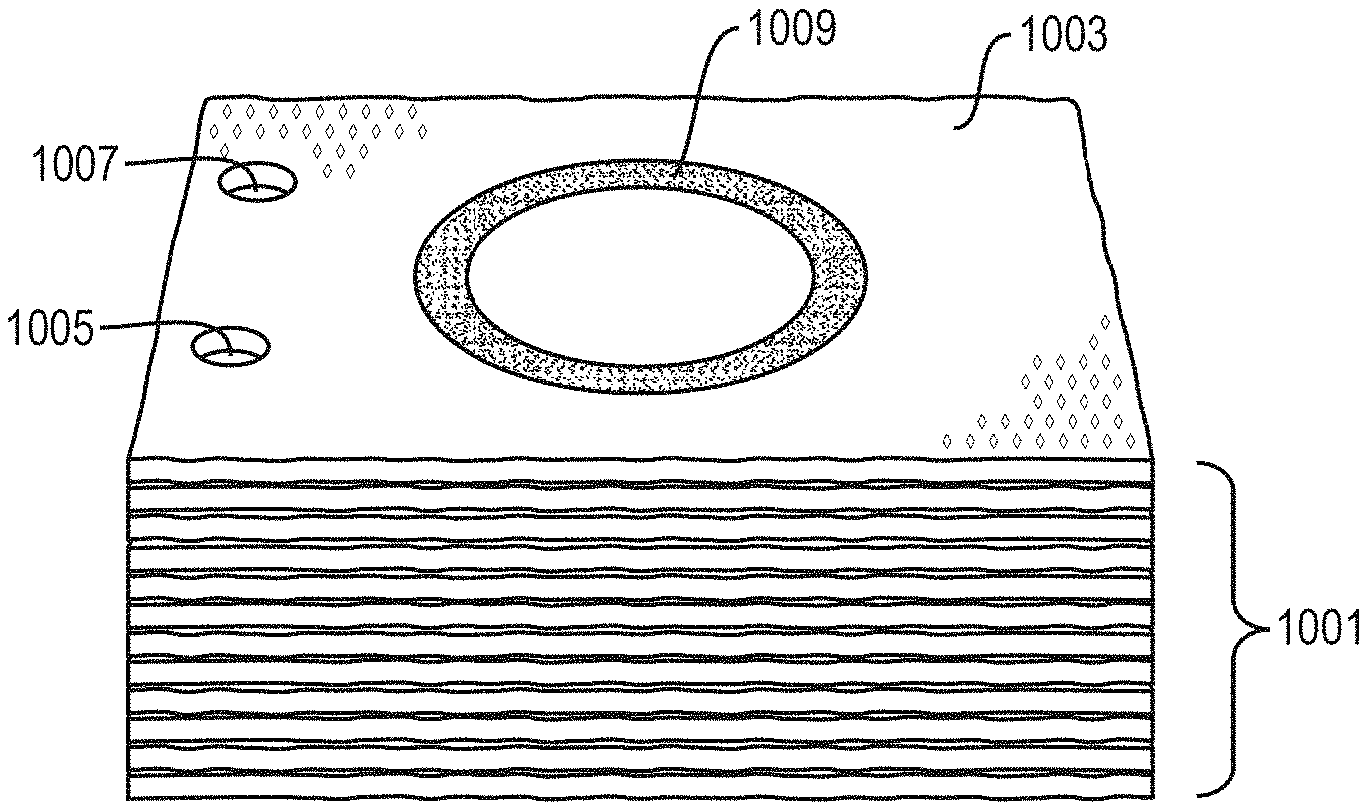
Invented by Robert Swartz, Buckley Crist, Eugene Gore, Joseph M. Jacobson, Impossible Objects Inc
Composites are materials made up of two or more different components that work together to create a material with superior properties. For example, carbon fiber reinforced polymers (CFRP) are composites made up of carbon fibers and a polymer matrix. These materials are known for their high strength-to-weight ratio, making them ideal for aerospace and automotive applications.
The market for methods to fabricate 3D print composites is driven by the need for lightweight, high-strength materials in various industries. The aerospace industry, in particular, has been a major driver of this market. The use of composites in aircraft has increased significantly in recent years, with Boeing and Airbus using composites extensively in their aircraft designs. The automotive industry is also a major player in this market, with companies such as BMW and Lamborghini using composites in their vehicles.
There are several methods for fabricating 3D print composites, each with its own advantages and limitations. One method is fused filament fabrication (FFF), which involves melting a thermoplastic filament and depositing it layer by layer to create a part. This method can be used to create composite parts by adding reinforcing fibers to the filament. However, the resulting parts may not have the same strength as those made using other methods.
Another method is continuous fiber reinforcement (CFR), which involves laying down continuous fibers in a specific pattern and then infusing them with a resin to create a composite part. This method can create parts with high strength and stiffness, but it is more complex and expensive than other methods.
The market for methods to fabricate 3D print composites is expected to continue growing as new applications are discovered and new materials are developed. The development of new materials, such as graphene and nanotubes, is expected to further increase the strength and durability of composites. Additionally, advancements in 3D printing technology, such as multi-material printing and faster printing speeds, will make it easier and more cost-effective to fabricate composite parts.
In conclusion, the market for methods to fabricate 3D print composites is a rapidly growing industry driven by the need for high-performance materials in various industries. As new materials and technologies are developed, the potential applications for 3D print composites will continue to expand, making it an exciting and dynamic market to watch.
The Impossible Objects Inc invention works as follows
A 3D object as per the invention consists of substrate layers that have been infiltrated with a hardened material. This is how the 3D object is made. This process can be repeated for all remaining substrate layers. Stack the substrate layers. The powder can be transformed into a substance which flows and then hardens into the hardened materials. The hardened material forms a pattern that infiltrates positive areas in the substrate layers, but does not infiltrate the negative regions. Preferably, the substrate is carbon fibre and any excess substrate is removed via abrasion.
Background for Methods to Fabricate Three-Dimensional Print Composites
Selective deposition of powder
EXAMPLE 1 (OF A SELECTIVE POWDER DEPOSIT)
EXAMPLE 2 – OF SELECTIVE POWDER DEPOSIT)
EXAMPLE 3 (OF A SELECTIVE POWDER DEPOSIT)
EXAMPLE #4 (OF SELECTIVE POWDER DEPOSIT)
General Observations (Selective Deposit of Powder)
Heat, Pressure
Removal Of Excess Substrate.
Thermoplastic and Thermosettable powder
Substrate/Removal Excess Substrate.
Registration
Substrate Layers
Rastering
Ink Jet Printer
Prototypes
Prototype #1
Prototype #2
Prototype #3
Many Ways to Implement Invention
Illustrative Implementation using Thermoplastic polymer powder
Click here to view the patent on Google Patents.