GENERATING SIMULATED WELD PATHS FOR A WELDING ROBOT
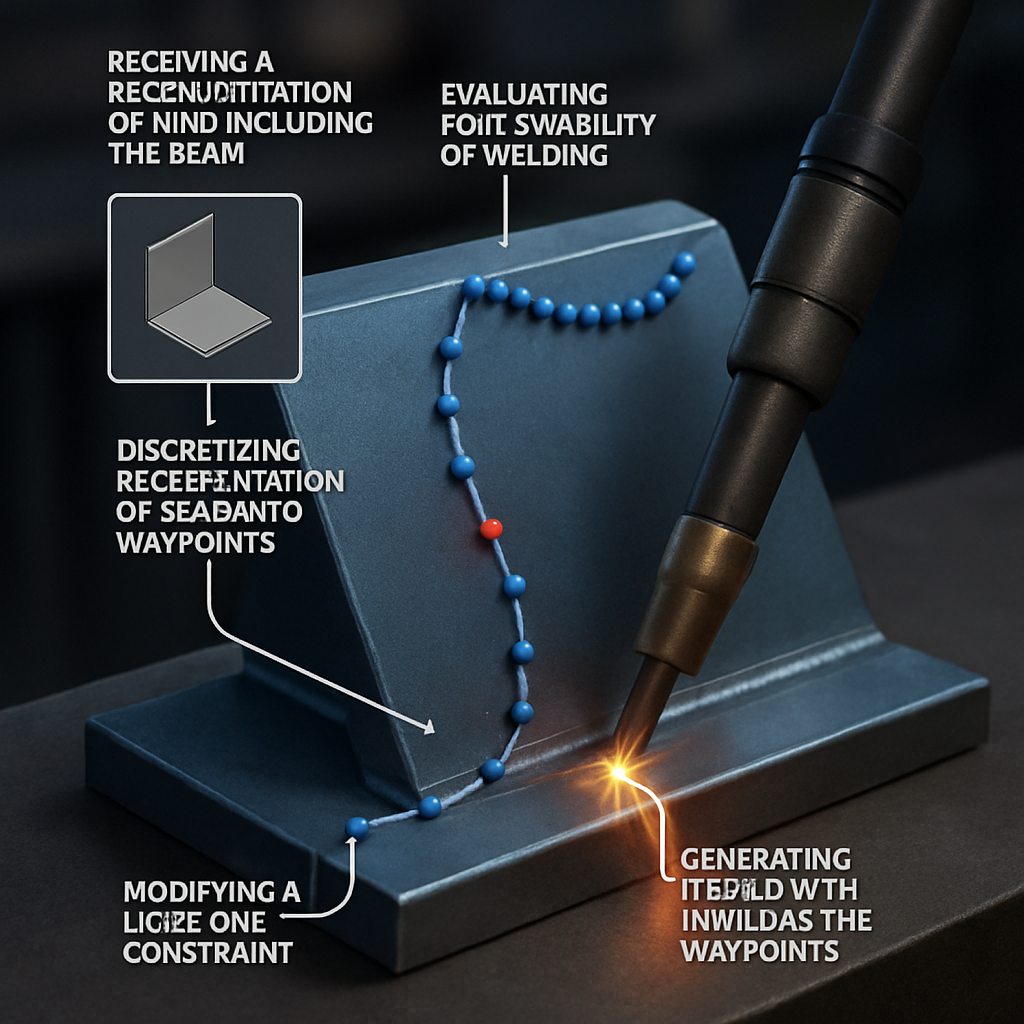
Invented by LONSBERRY; Alexander James, LONSBERRY; Andrew Gordon, KLEIN; Matthew, BALAJEPALLI; Surag, FENG; Chaojie, AGGARWAL; Rachit, SOOD; Raghav, Path Robotics, Inc.
The world of welding is changing fast. With robots taking over more jobs on factory floors, the need for smarter, safer, and more reliable welding is only growing. Today, we will explore a new patent application that introduces a smart way to plan and simulate weld paths for welding robots. This technology aims to make welding more efficient and less risky, while helping manufacturers save time and money. Let’s dive into how this invention works and why it matters.
Background and Market Context
Welding has always been a key part of manufacturing. From cars to bridges, welded joints hold our modern world together. For many years, most welding was done by skilled workers with years of experience. While human welders are talented, welding is a hard and sometimes dangerous job. The need for faster production and higher quality has led more companies to use robots for welding tasks.
Robotic welding is now common in many industries, including automotive, aerospace, appliances, and heavy machinery. Robots do not get tired or distracted, so they can work long hours without breaks. They also reduce workplace injuries and make it easier for companies to keep up with demand. With robots, manufacturers can make more products with fewer mistakes and less waste.
However, using robots for welding is not always simple. Robots need very exact instructions. They cannot “see” or “feel” their way around a part the way a human can. If a robot tries to weld a seam it cannot reach, it might crash into the part or itself, causing damage. Even worse, some seams are hidden or blocked, making it impossible for the robot to reach them safely. When this happens, the robot may leave parts unwelded or make bad welds, leading to quality problems and costly repairs.
Until now, most robotic welding systems have relied on computer models, like CAD (Computer Aided Design) files, to plan their welds. These models show where parts fit together and where seams need to be welded. Often, a user marks up the CAD model to show the robot where to weld. The robot then follows these instructions as best it can. But if the model does not show every obstacle, or if the robot’s arm cannot reach a certain spot, the robot may get stuck or even break something.
The need for better, safer, and smarter robotic welding has never been greater. Factories are getting more complex, and parts come in all shapes and sizes. Robots need to plan their moves carefully, so they can reach every seam without running into trouble. This is where the new patent application comes in. It offers a way to simulate weld paths ahead of time, so robots can avoid collisions and make better welds, even in tricky spots.
Scientific Rationale and Prior Art
To understand why this invention matters, let’s first look at how robotic welding planning has worked so far, and what challenges still exist.
In the past, welding robots used CAD models to plan out their welds. A user would mark up the model to show where welds were needed. The robot would then try to follow these paths. If the robot could not reach a seam, or if something was in the way, it might not realize there was a problem until it was too late. This could lead to incomplete welds, wasted parts, or even damage to the expensive robot itself.
Some robots use sensors to help them avoid collisions. These sensors can sometimes warn the robot if it gets too close to something. But often, the warning comes too late. The robot might already be in a bad spot, or it might not have any good way to finish the weld. Sometimes, the robot has to stop in the middle of a job, leaving the part unfinished.
A few advanced systems try to simulate the robot’s movements in advance. These systems use 3D models of the workspace and the robot, and they check for possible collisions. But even these systems have limits. They may not account for all the ways a robot’s arm can move, or they may not suggest new ways to get around obstacles. If a seam is blocked, the system might simply say, “This can’t be done,” and leave it at that.
Another problem is that welding is more than just moving the robot to the right spot. The angle of the weld head, the diameter of the welding tip, and the order in which seams are welded can all affect the quality of the weld. Changing these parameters can sometimes make the difference between a good weld and a bad one. But most systems do not suggest changes to these settings if a seam is hard to reach.
Up to now, the main approach has been to plan welds using fixed paths and settings, with little room for adjustment. If a seam is “unweldable,” the user might have to redesign the part or accept a lower quality weld. There has been a clear need for a system that can not only spot potential problems early, but also suggest ways to fix them—by changing the robot’s approach, adjusting weld parameters, or even suggesting different seams to weld.
The new patent application addresses these issues head-on. It builds on earlier systems that use CAD models and simulation, but it goes further by breaking each weld seam into many small steps and checking each one for possible problems. If an issue is found, the system can adjust its constraints, try different weld angles, or suggest alternative solutions. This gives manufacturers more options and helps robots do a better job, even with difficult parts.
This approach is more flexible and powerful than what has come before. It does not just say “yes” or “no” to a weld. Instead, it helps find a way to get the job done, with as few changes as possible. It also gives users a clear view of which parts of a seam can be welded and which cannot, using color-coded graphics to make it easy to understand. This makes life easier for engineers and helps factories avoid costly mistakes.
Invention Description and Key Innovations
Now let’s dig into the heart of the invention. What does it do, and how does it make robotic welding smarter and safer?
The core idea is to create a smart system that plans weld paths for robots by simulating every step in advance. The system starts with a digital model of the parts to be welded, usually a CAD file. It takes the seam to be welded and breaks it into many small pieces, called waypoints. Each waypoint marks a spot along the seam, and at each spot, the system considers different ways the robot’s weld head could be positioned.
Each of these positions is called a node. So, for each waypoint, there may be many nodes, each with a slightly different angle or orientation for the weld head. The system checks each node to see if it is possible for the robot to reach that spot without bumping into the part, the fixture, or itself. This is done using a digital simulation, often with 3D models of the robot, the workspace, and the part.
If the system finds that the robot would hit something at a certain node, it marks that node as “unweldable.” If all the nodes at a waypoint are unweldable, the system can try changing its approach. For example, it might relax some of its rules about the weld angle or try a different welding tip. It can also suggest moving the part using a motorized fixture, if available. The goal is to find a way for the robot to reach as many waypoints as possible without causing a collision or making a bad weld.
Once the system has checked all the waypoints and nodes, it plans out a full weld path for the robot. This path goes through all the weldable waypoints, using the best possible settings for each one. The system also tries to keep the robot’s movements smooth and efficient, so it spends less time turning or moving between spots. This helps the robot finish the weld faster and with better quality.
If some waypoints are still unweldable, the system lets the user know right away. It shows a color-coded display, with green for weldable spots and red for unweldable ones, so the user can see at a glance where the problems are. The user can then choose to try different weld settings, switch to a smaller weld head, or pick a different seam to weld. The system can simulate each of these options and show the results, making it easy to find the best solution.
This invention introduces several key innovations:
First, it breaks down each weld seam into small waypoints and nodes, allowing for a very detailed simulation of the robot’s path. This makes it much easier to spot potential problems and find ways around them.
Second, it uses a two-step process to check each node: first, it checks if the robot can reach the spot (kinematic feasibility), and then it checks if the robot would hit anything (collision detection). This makes the system both fast and accurate.
Third, it can adjust its constraints and try different weld parameters if a waypoint is unweldable. This means the system can often find a solution even in tricky situations, without needing to redesign the part or change the production line.
Fourth, it gives users a clear, visual way to see which parts of a seam are weldable and which are not. This helps engineers make better decisions and avoid surprises on the factory floor.
Finally, it can store all the simulation data, weld paths, and user choices, making it easy to keep track of what has been tried and what works best. This data can be used to improve future welds and share best practices across the company.
The system is designed to work with many kinds of welding robots and setups. It can use motorized fixtures to move parts, different types of weld heads, and many types of welds (arc, spot, TIG, and more). It is flexible enough to be used in small shops or large factories, and it can help both expert welders and less experienced users get better results.
Conclusion
Robotic welding is a big part of modern manufacturing, but it comes with its own set of challenges. Planning safe, efficient, and high-quality welds is not easy, especially when parts are complex or space is tight. The new patent application we have explored today offers a smarter way to plan robotic welds. By simulating every step in advance and allowing for flexible adjustments, it helps robots avoid collisions and make better welds, while giving users more control and insight.
This invention stands out because it does not just flag problems—it helps solve them. It gives manufacturers the tools they need to get more value from their welding robots, reduce downtime, and improve product quality. As factories become even more automated and complex, smart planning systems like this will become even more important. If you are involved in manufacturing, robotics, or welding, this technology is worth watching. It could help your business save time, cut costs, and stay ahead in a fast-changing world.
Click here https://ppubs.uspto.gov/pubwebapp/ and search 20250217543.