DUAL REACTOR SYSTEM FOR DECONTAMINATION AND CONVERSION OF PLASTIC DERIVED OIL TO HYDROCARBON INTERMEDIATES
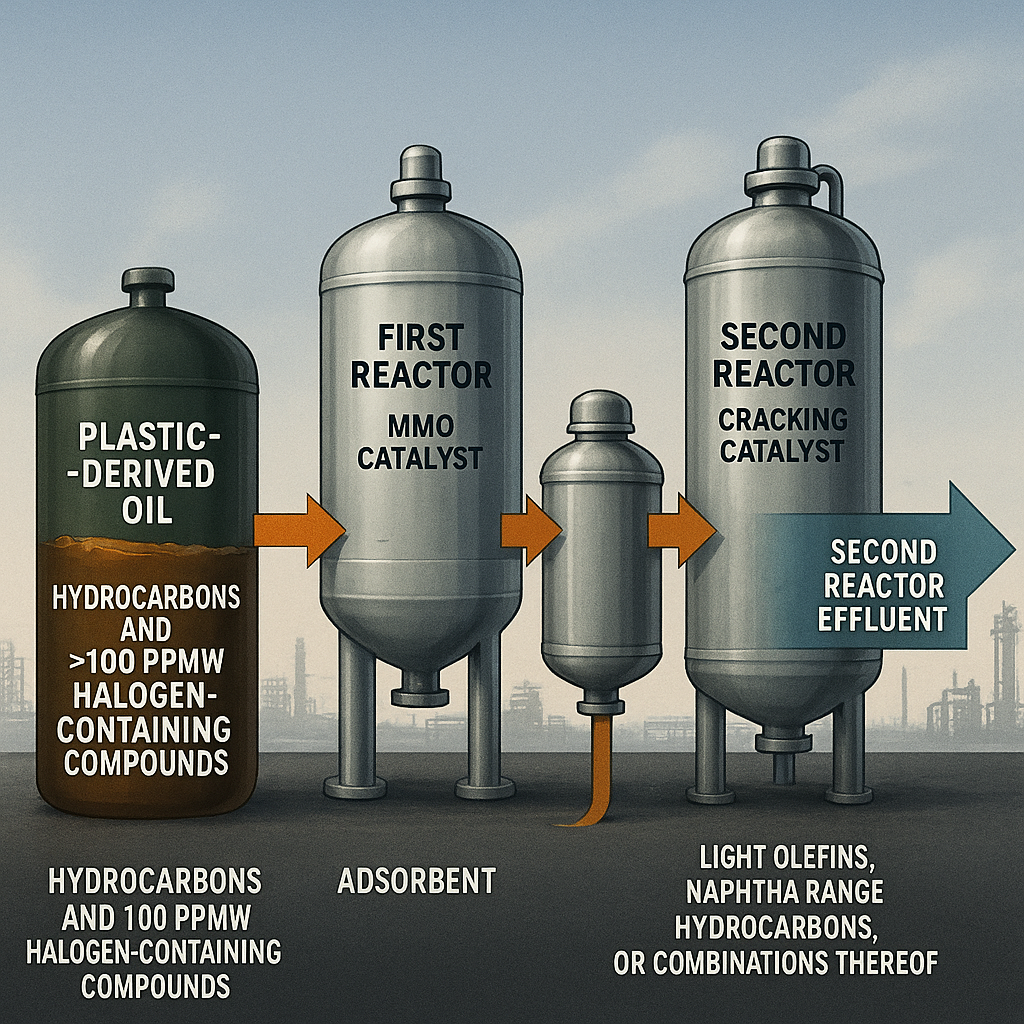
Invented by Akah; Aaron Chi, Aleisa; Rashed, Jazzar; Ahmad, Saudi Arabian Oil Company
Plastic waste is a growing problem. But what if that waste could be turned into something valuable? Today, we are exploring a new process for upgrading plastic derived oil. This process helps turn old plastic into useful fuel and chemicals. Let’s break down how it works, why it matters, and what makes it special.
Background and Market Context
Plastic is everywhere. It’s in bottles, bags, toys, and even cars. We use a lot of it every day. As a result, we also throw away a lot. This waste is a big challenge for cities and countries around the world. Most plastic does not break down quickly. Instead, it lasts for hundreds of years. This means landfills are filling up, and oceans are getting more polluted.
Many people and companies are looking for ways to recycle or reuse plastic waste. Some plastics are easy to recycle, like bottles and food containers. Others, such as bags or mixed plastics, are much harder. In recent years, one idea has become more popular: turning plastic waste into oil through a process called pyrolysis. This oil can then be used as a fuel or as a building block for new chemicals.
But there’s a problem. The oil made from plastic waste is not very clean. It can contain unwanted chemicals, like halogens (especially chlorine), which come from plastics like PVC. These chemicals make the oil hard to use. They can cause damage to machines, poison catalysts in refineries, and make it hard to meet fuel standards. If not removed, halogens can also harm the environment when the oil is burned.
There is a growing need for a process that can clean up plastic derived oil. If we can do this, we can turn plastic waste into valuable products—like gasoline, diesel, or even the raw materials for making new plastics. This can help reduce pollution, cut down on carbon emissions, and create a more “circular” economy where waste becomes a resource.
The new process described in this patent application is designed to solve these problems. It helps remove the bad chemicals from plastic derived oil. It also turns the oil into even more valuable products, like light olefins and naphtha, which are used to make plastics and fuels. Let’s look at the science behind this process, and how it stands out from what has been done before.
Scientific Rationale and Prior Art
To understand why this invention is important, we need to look at how plastic is usually recycled and what happens when it is turned into oil.
When plastic is heated in a process called pyrolysis, it breaks down into smaller pieces. These pieces can be gases, liquids (oil), or solids (char). The oil is the main product people want. It contains hydrocarbons—molecules made of hydrogen and carbon—that can be used as fuel or chemical feedstocks.
However, most plastics contain additives. Some plastics, like PVC, have chlorine in their structure. During pyrolysis, these additives and halogens end up in the oil. The oil can also have a wide range of boiling points, from very light to very heavy parts. This makes it hard to process in existing refineries.
Refineries use catalysts to turn crude oil into fuels and chemicals. But the halogens in plastic derived oil can poison these catalysts. For example, chlorine can turn into hydrochloric acid (HCl), which corrodes metal pipes and damages equipment. It can also cause the formation of salts that block pipes and heat exchangers. If halogens get into the final fuel, they can harm engines and increase pollution.
People have tried various ways to clean plastic derived oil. Some use water washing to remove salts and polar impurities. Others use adsorbents—materials that “soak up” bad chemicals. There are also processes that use special catalysts to remove halogens before the oil is used further. However, these methods often are not complete, or they are too expensive or complicated for large-scale use.
There is also a need to turn the cleaned oil into more valuable products. Catalytic cracking is a common way to break large hydrocarbon molecules into smaller, more useful ones, like gasoline or light olefins (ethylene, propylene, butenes). But again, if the oil is not clean, the catalysts used in cracking will not last long.
Some earlier inventions tried to combine dehalogenation (removing halogens) with upgrading the oil. They often used separate steps, different reactors, or even required that the plastic waste be sorted very carefully before processing. Many of these methods are not flexible enough to handle mixed plastic waste or do not fully solve the contamination problem.
This brings us to the new process described in the patent application. It builds on what has come before but introduces several key improvements. It uses a two-step reactor system. The first reactor uses a special mixed metal oxide catalyst to remove halogens and other contaminants. The second reactor uses a different catalyst to crack the cleaned oil into light olefins and naphtha. The process also allows for easy regeneration of the catalysts, making it practical for continuous, large-scale use.
Let’s examine exactly how this process works and what makes it innovative.
Invention Description and Key Innovations
The heart of this invention is a process and a system for upgrading plastic derived oil. The process is designed to take oil made by melting and breaking down waste plastic and turn it into cleaner, more valuable products. Here’s how it works, step by step, in simple terms:
Step 1: Making the Plastic Derived Oil
The process starts with mixed plastic waste. It can be a blend of many types of plastics, including those that are hard to recycle. The plastic is first melted and treated in a dehalogenation unit. This step helps get rid of some of the halogens (like chlorine) by heating the plastic and allowing gases like HCl to escape. The gases are scrubbed away. The melted plastic then goes into a pyrolysis reactor, where it is heated even more. This breaks the long plastic chains into smaller hydrocarbons, forming a liquid oil.
Step 2: Dehalogenation and Decontamination in the First Reactor
The plastic derived oil from pyrolysis still contains some halogen compounds and other unwanted chemicals. It is sent into the first reactor. Here, the oil is mixed with a special catalyst made from mixed metal oxides (MMO). This catalyst has different metal oxides like iron, zirconium, cerium, aluminum, titanium, calcium, silicon, sodium, and magnesium. These oxides work together to react with the halogen compounds in the oil. They help turn the halogens into hydrogen halides (like HCl), which are then trapped by the catalyst itself. The result is a liquid stream with much lower levels of halogen-containing compounds—often less than 100 parts per million.
What makes this step special is the use of the MMO catalyst. Traditional methods might use only one type of oxide, but this process uses a blend. The metals are mixed together in each catalyst particle, not just coated on the outside. This gives the catalyst more surface area and makes it better at removing halogens. Sometimes, the catalyst is made from industrial byproducts (like red mud from aluminum making) or special mixtures made by co-precipitation. The catalyst can be in the form of small particles or pellets, designed for use in fluidized bed reactors, which are common in oil refineries.
The first reactor can be a fixed bed or a fluidized bed. In a fluidized bed, the catalyst and oil move together through the reactor, which helps keep the process going without stopping for maintenance. The catalyst can be regenerated by burning off any coke (carbon deposits) in a regenerator unit and then separated by density from other catalysts for reuse.
Step 3: Further Cleanup Using Adsorption
Even after the first reactor, some halogen-containing compounds might remain. The oil is sent through an adsorption unit, where it passes over materials like alumina, zeolites, or activated carbon. These materials “catch” any leftover bad chemicals, making the oil even cleaner. This ensures that the oil meets strict standards before further processing.
Step 4: Separation of Oil Fractions
After adsorption, the oil can be separated into lighter and heavier parts. The light fraction (mainly gases or very light liquids) can be collected directly. The heavier fraction, which contains most of the useful hydrocarbons, is sent to the next step.
Step 5: Cracking the Oil in the Second Reactor
The heavy, cleaned oil is sent into a second reactor. Here, it is mixed with a different catalyst—often a zeolite type, like USY or ZSM-5. This catalyst helps break the large hydrocarbon molecules into smaller, more valuable ones. The main products are light olefins (like ethylene and propylene), naphtha (used to make gasoline or as a chemical feedstock), and sometimes light aromatics (like benzene, toluene, xylenes). The process uses high temperatures (500°C to 650°C) and is done in a fluidized bed reactor for continuous operation.
After cracking, the products are separated in a product separation system. This system sorts the different hydrocarbons into streams that can be sold or used to make new products. The process is flexible—it can be adjusted to make more of a certain product, depending on market needs.
Step 6: Catalyst Regeneration and Recycling
Both the first and second reactors use solid catalysts. Over time, these catalysts get covered with coke and lose effectiveness. The process includes a single regenerator, which burns off the coke from both types of catalysts at the same time. After regeneration, the catalysts are separated by density and returned to their respective reactors. This recycling step makes the process efficient and cost-effective.
Step 7: Optional Pre-Treatment
If the plastic derived oil contains very high levels of halogens or other contaminants, there are extra steps that can be added. The oil can be washed with water to remove salts and polar chemicals. Then, it can go through an upstream adsorption unit for even more cleanup. The process uses sensors and a control system to decide when these extra steps are needed. If the halogen level is below a set point (like 100 ppm), the oil goes straight to the first reactor. If it’s higher, it gets the full treatment before entering the main process.
Key Innovations and Advantages
This process stands out for several reasons:
1. Complete Halogen Removal: The mixed metal oxide catalyst is very effective at pulling out halogens, especially chlorine. This protects refinery equipment and downstream catalysts, making the process safer and more reliable.
2. Flexible Feed Handling: The process can handle mixed plastic waste, not just sorted or pure types. This reduces the cost and complexity of collecting and preparing the plastic feed.
3. Efficient Catalyst Management: Using a single regenerator for both types of catalysts and separating them by density keeps the system simple and efficient. The catalysts can be regenerated many times, lowering operating costs.
4. High Value Products: The cleaned oil can be cracked into light olefins and naphtha, which are in high demand for making new plastics and fuels. The process also produces less unwanted heavy oil or residue.
5. Smart Control: Built-in sensors and control systems ensure the process adapts to changes in the feedstock. This means it can run continuously and handle variations in the quality of the plastic waste.
6. Integration with Existing Refineries: The reactors and equipment used are similar to those already found in petroleum refineries. This makes it easier to add the process to existing plants, speeding up adoption and reducing costs.
7. Environmental Benefits: By turning plastic waste into valuable products and reducing the need for fossil fuels, the process helps cut greenhouse gas emissions and keeps plastic out of landfills and oceans.
Performance and Results
Tests of the process show that it can reduce halogen levels in plastic derived oil to below 100 ppm, and even lower after adsorption. When the cleaned oil is cracked, it produces high yields of light olefins and naphtha. For example, at cracking temperatures of 600°C, the oil can yield over 20% ethylene and propylene, plus a large amount of naphtha. Heavy residues are kept very low. The products meet the standards needed for further processing or direct use.
This means that, for the first time, mixed plastic waste can be turned into high-quality fuels and chemicals on a large scale, using existing refinery technology with only a few new additions.
Conclusion
The new process for upgrading plastic derived oil is a big step forward in plastic recycling. It takes mixed, dirty plastic waste and turns it into clean, valuable products. The process uses a smart combination of mixed metal oxide catalysts, adsorption, and catalytic cracking. It is flexible, efficient, and ready to be used in today’s refineries.
This invention helps solve several problems at once: it deals with plastic waste, protects the environment, and creates valuable chemicals and fuels. It is a strong example of how smart engineering and chemistry can turn a challenge into an opportunity. For companies, cities, and anyone concerned about plastic pollution, this process offers a new path forward—one where waste is not a problem, but a resource.
Click here https://ppubs.uspto.gov/pubwebapp/ and search 20250215336.