CELL TEST APPARATUS AND METHOD OF MANUFACTURING CELL TEST APPARATUS
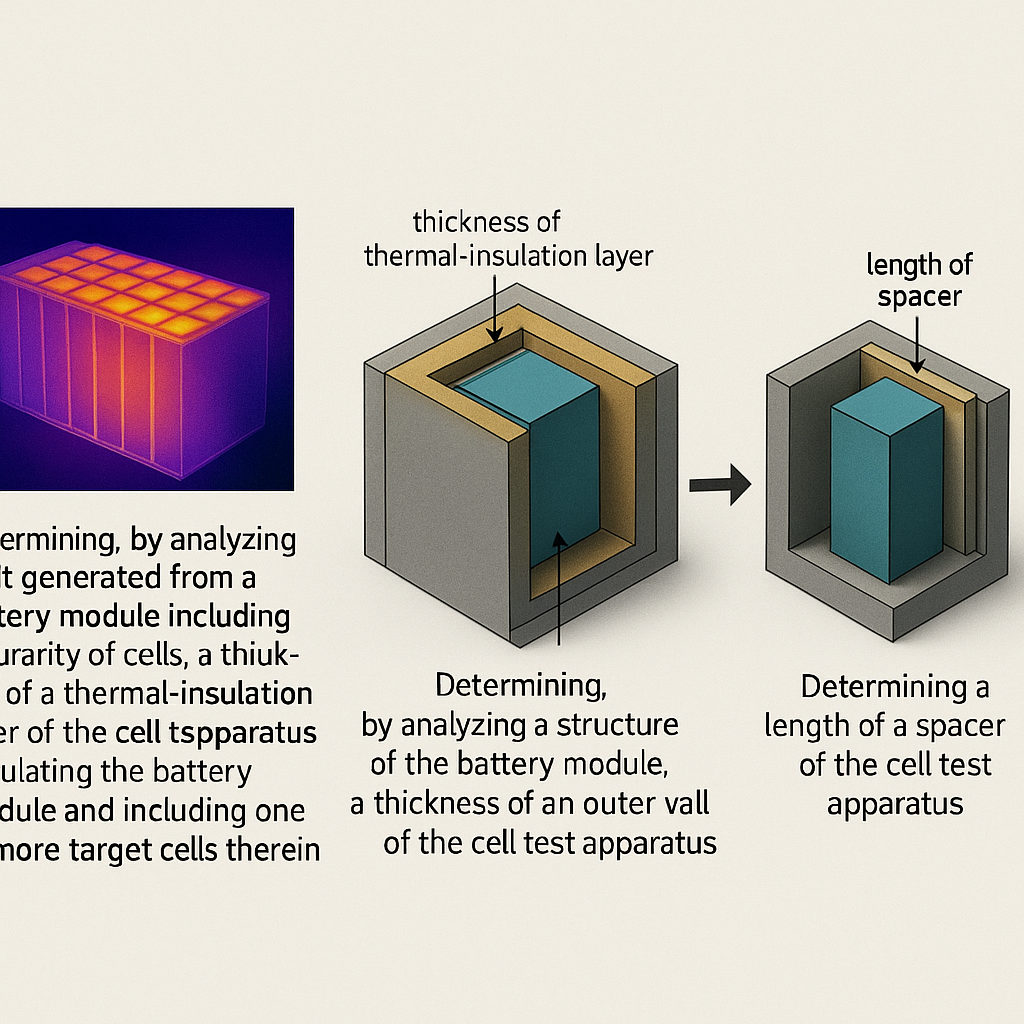
Invented by KIM; Jin, AHN; Gijang, PARK; Jongtaek, KIM; Hyunsung, SHIN; Eunseon
Battery technology is everywhere. It powers our phones, cars, and even solar power systems. At the heart of it all are secondary batteries, like lithium-ion, that can be charged and used over and over again. But how do we know if these batteries are good, safe, and will last a long time? The answer lies in special tools called cell test apparatus. Today, we’ll explore a new patent that helps make these tools better, more accurate, and more reliable. Let’s dive into how this new method works, why it’s important, and what makes it different from old ways.
Background and Market Context
Batteries are a big part of modern life. Every time you use your phone, drive an electric car, or store energy from the sun, you’re using a secondary battery. These are batteries that can be recharged. The most popular kind is the lithium-ion battery. They are everywhere because they store a lot of energy and can be charged quickly.
But here’s the problem: not all batteries are the same. Some last longer. Some are safer. Some can be charged faster. Companies and engineers need to test these batteries to make sure they work well in the real world. This is where cell test apparatus come in. These are special devices that test one or more battery cells and give information about how much energy they can hold, how long they last, or how safe they are.
Testing is very important. If you don’t test well, a battery that looks good in the lab might fail in your car or phone. This could mean your phone dies too quickly, or worse, your car’s battery overheats. To avoid these problems, companies use cell test apparatus to check batteries before they’re used in real products.
But current cell test apparatus have some problems. Sometimes, they don’t match the real conditions that batteries face when they are packed together in a big module, like inside a car battery pack. This can lead to wrong results. For example, a battery that looks perfect in a test might act very differently when it’s inside a real module with many other cells around it. This is because things like heat and stress change when many cells are together. If the test apparatus doesn’t copy these conditions well, the test results may be wrong or unreliable.
Because battery-powered devices are everywhere now, and because safety and performance are so important, there is a huge need for better testing tools. Companies want to know exactly how a battery will behave in real life, not just in the lab. That’s why making cell test apparatus that closely match real battery module conditions is so important. This also helps companies make batteries that are safer, last longer, and give better performance.
In summary, the battery market needs better ways to test batteries. The old ways can’t always keep up. New methods and tools are needed to make sure batteries are safe, strong, and ready for the real world. The patent we’re discussing introduces a new way to make cell test apparatus so they can give more real and accurate results.
Scientific Rationale and Prior Art
To understand why this new invention matters, let’s look at how batteries are tested today and what the problems are.
When a battery cell is tested, it’s often done alone, in a special chamber. The test checks things like how much energy the cell can store, how many times it can be charged and discharged, and how hot it gets. But in real life, battery cells are packed together in modules. In a car, for example, there may be dozens or even hundreds of cells tightly packed. When cells are close together, they get hotter and can press against each other. This can affect how they work and how long they last.
Traditional cell test apparatus usually don’t copy these real-world conditions very well. For example, the insulation (material that keeps heat in or out) around each cell in the test device may not match what happens inside a real module. The walls of the test chamber may not be as thick or made of the same material as the ones holding the cells in a real battery pack. There may be gaps or spaces that are different. Also, the way heat and pressure build up in the test may not match what happens in a real module.
This means that even if a cell passes the test in the lab, it might fail or behave differently when it’s inside a real battery module. For example, it may get hotter than expected, or it may not last as long. This is a big problem for companies making batteries, because they want to know how their products will really work.
Some older inventions tried to solve these problems by making test chambers thicker or using different materials. Others tried to add more insulation or copy the shape of real battery modules. But these solutions were not perfect. They often didn’t look closely at things like:
– The exact amount of heat a battery module produces
– The way pressure builds up inside a real battery module when many cells are packed together
– The real distance between cells in a module
Most old test apparatus just guessed at these numbers or used one-size-fits-all designs. They didn’t take measurements from real battery modules and use those numbers to design the test device. As a result, their testing was not as accurate as it could be.
Another problem was that older test methods didn’t let users adjust the test device based on the actual battery module they wanted to copy. For example, if a company made a new battery module with different spacing or different materials, the old test device might not match it. This made testing less useful.
There was also a lack of good ways to decide how thick the insulation or the test chamber walls should be. Should the insulation be 10mm thick? 20mm? The old methods didn’t have a clear way to decide. This led to a lot of guesswork.
In short, the science behind old cell test apparatus didn’t match the real-world needs very well. There was a need for a clear, step-by-step method to design a test device that really copies the heat, pressure, and spacing found in real battery modules. This would help companies get more accurate test results and make better batteries.
Invention Description and Key Innovations
This new patent introduces a smarter way to make cell test apparatus. The goal is to make the test device copy a real battery module as closely as possible. This way, the test results will be much closer to what happens in real life. Here’s how the new invention works and what makes it special.
The process starts by looking at the real battery module that the user wants to copy. The team carefully measures how much heat the module produces during use and how much pressure builds up inside when the cells are packed together. They also measure the exact distance between each cell. All these numbers are then used to design the test device.
Step 1: Determining Thermal-Insulation Layer Thickness
First, the team finds out how thick the thermal-insulation layer should be. This is the part of the test device that keeps heat in or out. They do this by running the real battery module through charge and discharge cycles and measuring the temperature at key spots, like the vent of each cell. They record this as the first temperature. Then, they test the cell inside the test device and measure the temperature again. The goal is to adjust the insulation thickness so that the temperature inside the test device matches as closely as possible (between 90% and 100%) to the real module. This is repeated with different insulation thicknesses until the right one is found. This is a big improvement over guessing or using a standard thickness for every test.
Step 2: Determining Outer Wall Thickness
Next, they look at the outer walls of the test device. In a real battery module, there’s pressure on the cells from being squeezed together. This pressure can change how the cells work. The team measures the pressure (called stress) at different points in the real module, like at the ends and at the center. They then decide on a target pressure for the test device, which is usually between the highest and lowest pressures measured. The thickness of the test device walls is then set so that the same pressure is applied to the cells during the test. The material used for the wall, like stainless steel, is chosen to match the real module as well. This step helps make sure the test device copies the real life squeezing and pressure that happens inside a battery pack.
Step 3: Determining Spacer Length
The team then looks at the distance between each cell in the real module. This is important, because if the test device puts the cells too close or too far apart, the heat and pressure will be different. By measuring the real distance and adding in the thickness of the insulation and walls, they can set the length of the spacers in the test device. This makes sure everything is spaced just like in the real battery module.
Assembly of the Test Apparatus
Once all these measurements are done, the test device is built. It includes:
– An insulation layer that sits right next to the cell
– One or two thermal-insulation layers (made from materials like Bakelite) on both long sides
– Strong outer walls (often stainless steel) outside the thermal-insulation layers for pressure
– Spacers on the short sides to keep everything in place
– A cooling unit on the bottom, just like in real battery modules, to keep the temperature controlled
The insulation layer might be a special sheet with sticky sides to help hold everything together. Everything is sized to match the real module as closely as possible. The cooling unit even uses the same temperature as the real module to make tests fair.
Why Is This Better?
This new method is better because it takes real measurements from the battery module and uses them to design the test device. Instead of guessing, it copies the real world. This means that when you test a battery cell in this device, you get results that are almost the same as what you would get if you tested the cell inside a real module. This helps companies trust their tests more and avoid surprises later.
Tests done with this new method have shown that the results are much closer to those from real modules. For example, after many charge and discharge cycles, the test device gave capacity numbers that matched the real module much better than older test devices. This means you can trust the test results and know how the battery will perform in the real world.
Other smart touches include using materials like Bakelite for insulation (which is very good at stopping heat) and stainless steel for the walls (which is strong and hard to bend). The test device can also be built with just one cell or many cells, depending on what needs to be tested.
The method also allows the test device to be customized for different modules. If a new battery module design comes out, the team can just measure the heat, pressure, and spacing, and build a new test device that matches. This flexibility is very useful as battery technology keeps changing.
Finally, the patent gives a clear, step-by-step guide to making the test device. It tells exactly how to measure, what numbers to use, and how to build each part. This takes away the guesswork and makes it easy for companies to get accurate, repeatable results.
Conclusion
The battery world is changing fast, and testing needs to keep up. This new patent gives a better, smarter way to make cell test apparatus. By using real data from battery modules, it makes test results more accurate and useful. Companies can now test their batteries and know with confidence how they’ll work in real devices, from phones to cars.
This new method helps everyone—engineers, companies, and end users—by making batteries safer, longer-lasting, and more reliable. It’s a big step forward in battery testing, and it will help power the future of technology.
Click here https://ppubs.uspto.gov/pubwebapp/ and search 20250216194.