Invention for Carbon dioxide Treatment of Concrete Upstream from Product Mold
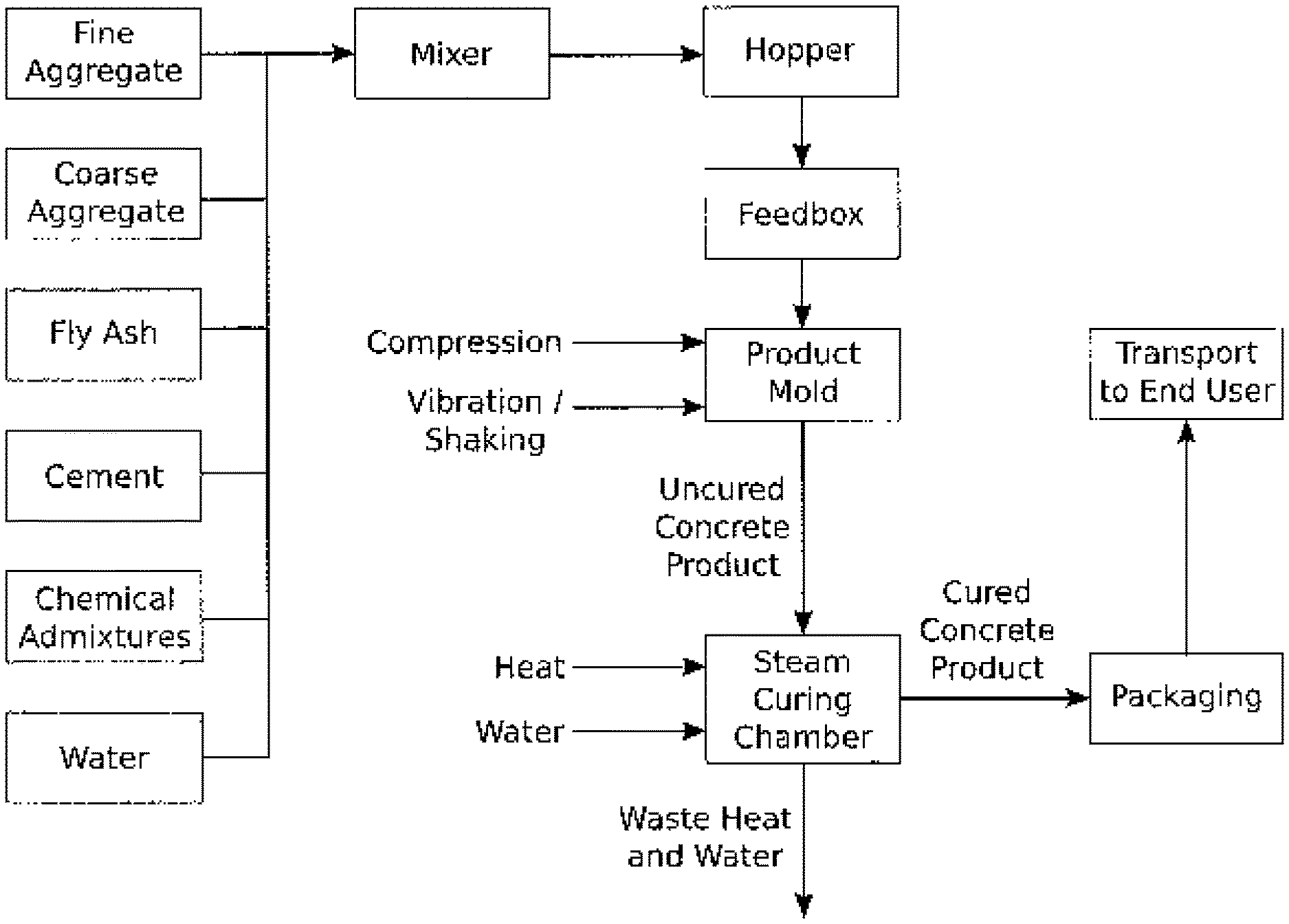
Invented by Robert Niven, George Sean Monkman, Dean Paul Forgeron, Carboncure Technologies Inc
The market for carbon dioxide treatment of concrete is driven by several factors, including the increasing demand for sustainable building materials, the need for stronger and more durable concrete products, and the growing awareness of the environmental impact of traditional concrete production methods.
One of the key benefits of carbon dioxide treatment of concrete is its ability to reduce the carbon footprint of the construction industry. Traditional concrete production methods are responsible for a significant amount of carbon emissions, which contribute to climate change. By using carbon dioxide as a curing agent, the carbon footprint of concrete production can be significantly reduced.
Another benefit of carbon dioxide treatment of concrete is its ability to improve the strength and durability of concrete products. Carbon dioxide reacts with the calcium hydroxide in the concrete mix to form calcium carbonate, which fills in the pores and voids in the concrete and makes it stronger and more resistant to damage.
The market for carbon dioxide treatment of concrete is also driven by the increasing demand for sustainable building materials. As more and more consumers become aware of the environmental impact of traditional building materials, they are seeking out more sustainable alternatives. Carbon dioxide treatment of concrete is a perfect example of a sustainable building material that offers numerous benefits over traditional concrete.
In conclusion, the market for carbon dioxide treatment of concrete upstream from product mold is a rapidly growing industry that is driven by the need for sustainable building materials, stronger and more durable concrete products, and the growing awareness of the environmental impact of traditional concrete production methods. As more and more consumers seek out sustainable building materials, the demand for carbon dioxide treatment of concrete is expected to continue to grow in the coming years.
The Carboncure Technologies Inc invention works as follows
Fresh Concrete is treated with Carbon Dioxide prior to delivery to the product mold to form concrete products. The carbon dioxide gas is directed upstream of the product mold through a manifold that may be attached to a feedbox, hopper or other device. “Treating the concrete in its loose state with carbon dioxide gas prior to placing it in the mold can generally promote uniform and enhanced CO2 uptake.
Background for Carbon dioxide Treatment of Concrete Upstream from Product Mold
The following paragraphs do not admit that the information discussed is part of prior art, or the knowledge of people skilled in the arts.
U.S. Pat. No. No.
U.S. Pat. No. No. 4,362,679, (Malinowski), describes a way to cast different types of concrete without using an autoclave or curing chamber after mixing. The concrete is cast and then externally or internally treated with a vacuum to de-water and compact it. Carbon-dioxide is then supplied to the mass under a low pressure so that it diffuses into capillaries in the concrete mass.
U.S. Pat. No. 5,935,317 (Soroushian et al.) This patent describes the use of CO2 as a pre-curing agent prior to the rapid (steam) curing process of cement or concrete products. It is intended to prepare the product to be able to withstand high temperatures and high vapor pressures in an accelerated curing environment, without microcracking.
U.S. Pat. No. 7,390,444 (Ramme et al.) The process described in the patent is for removing carbon dioxide from flue gases emitted by combustion chambers. The process involves forming a flue gas foam, adding the foam to a cementitious mixture (e.g. fly ash), and then foaming the mixture. The foamed material is then allowed to dry, preferably into a controlled-low-strength product with a compressive force of 1200 psi. Carbon dioxide from flue gases and waste heat reacts to increase the strength of the controlled low-strength materials. The carbon dioxide is captured in this process. The CLSM is a lightweight material that can be crushed into pellets or crushed to form an aggregate similar to pumice, a naturally occurring mineral.
U.S. Pat. No. 8,114,367 (Riman et al.) This patent describes a method for sequestering greenhouse gases, which includes: (i), providing a solution containing a first reagent capable of reacting to a green house gas; (ii), contacting the solution to a green house gas under conditions promoting a reaction to produce a at minimum a 1st reactant, (iii), providing a porous matrices with interstitial space and containing at a least 2nd reactant, (iv),
International Publication No. WO/2012/079173 (Niven et al.) describes carbon dioxide sequestration in concrete articles. Concrete products, such as blocks, substantially plane products (such a pavers), and hollow products, (such a hollow pipes), are formed using molded concrete while carbon dioxide is injected through perforations into the concrete.
INTRODUCTION
The following paragraphs were written to introduce readers to the detailed description which follows, and not to limit or define the subject matter claimed.
According to one aspect of the disclosure, a concrete product forming method may include: supplying new concrete; treating it with carbon dioxide to form treated cement; and delivering the treated concret to a mold designed to form concrete products after the treatment step.
According to one aspect of this disclosure, an apparatus to form concrete products can include: a mold for the concrete product; a component located upstream from the mold and designed to treat fresh concrete using carbon dioxide to create treated concrete and to deliver the treated concrete either directly or indirectly to a mold; and finally, a gas distribution system that is connected to the component, and designed to control the distribution of carbon dioxide through the component.
According to one aspect of the disclosure, the process for accelerating the curing and sequestering CO2 in concrete can include: supplying new concrete; directing multiple flows of CO2-containing gas under pressure to the fresh concrete, at various locations, to create treated concrete; and, following the step of direction, delivering treated concrete to a mold.
The following examples will reveal to those who are ordinarily knowledgeable in the art other aspects and features of this disclosure.
The following examples of embodiments of claimed inventions describe various apparatuses and methods. The examples below do not limit any claimed invention. Any claimed invention can cover apparatuses or methods that are different from those described. Claim inventions do not limit themselves to only those apparatuses or techniques that have all the features described in the following apparatus or method, or features shared by multiple or all the described apparatuses or processes. An apparatus or method described in this document may not be an embodiment of a claimed invention. “Any invention disclosed in the apparatus or method described in the document that is not claimed may be covered by another protective instrument. The applicant(s), the inventor(s), and/or the owner(s), do not intend abandonment, disclaimer, or dedication to the public of any such invention.
Referring to FIG. Concrete products or concrete articles can be commercially produced by using a mold machine to form them and then curing. In a typical concrete plant, different ingredients are transported to a mixer in order to produce fresh concrete. Ingredients include, for instance, fly ash cement, water, fly ash and coarse aggregate. Fresh concrete is mixed and transferred into a hopper above the product mold.
In every production cycle, a certain quantity of concrete from the hopper is poured into the product mould. In the product mould, concrete can be compacted and formed into multiple products. The products can be transported to the curing area on a tray that is removed from the mold machine. Exposure to the air can cure products slowly (7-30 days). In some commercial operations the products can be quickly cured by heat or steam curing. Products may be placed for 8-24 hours in a chamber that uses steam to cure. The cured product is removed from the curing zone and sent to other processing stations for packing and transporting to the end-user.
Some production sequences use a feedbox. In every production cycle, a certain quantity of concrete from the hopper is transferred to the feedbox which is located above the product mould. As part of the regular cycle, the material from the feedbox goes into the product mould. The cycle is restarted once the product mold has been filled and the finished product is ready. A grid of agitators can be placed in the feedbox so that the concrete is agitated as it drops from the feedbox and into the molding machine. As described earlier, the concrete is formed and compacted within the product mold.
In certain cases, dry cast concrete can be poured into the feedbox when it is in the retracted position. The feedbox can then be moved from a retracted to an extended position. It is then arranged on top of an open product mold. Gravity can then deposit the dry cast concrete from the feedbox in the product mold. The feedbox can be moved from its extended position back to the retracted one after the dry cast concrete has been deposited into the product mould. The grid can be placed to impact the concrete in feedbox and help the concrete pass uniformly into the product mould.
These processes can be used with a variety of concrete products, including but not limited, to blocks, pavers and other decorative or structural masonry components, tiles, pipes, etc.
In the process of forming concrete block, for instance, a pallet can be moved onto a pallet tray or table by a conveyor. The pallet is then moved upwards until it contacts the product mould and forms the bottom of each of its cavities. The feedbox can be retracted or extended, causing the feed drawer to open over the frame of the product mould. The concrete is dropped in the product mould with the help of the agitator grid. It fills one or more cavities via the top opening. Optionally, the product mold can be filled while vibrating. The block molding machine can include a blade or cutoff bar that is fixed to the feedbox to remove excess dry cast concrete on the top of one or more cavities when the feedbox returns to its retracted position. The block molding machine can include a stripper with a compaction arms and at least one shoe that is able to be moved through the open tops of the cavities to compress the dry-cast concrete to the desired psi rating (pounds per square inch), while vibrating the headshoe, the product mold, the pallet and/or the pallet table. While the stripper assembly remains in its lowered position, the form can be raised and the concrete blocks left on the table. The compaction arm can then be raised to allow the blocks to be ejected on the table from the mold machine. The cycle is repeated as the table with the formed blocks travels along a conveyor into the steam chamber.
In general, a concrete block production cycle involves several steps that are performed within a short time period with the mold machine. Every production cycle can only make a few blocks (for example, 1 to 16 or even more), but it only lasts a short time (5 to 12 seconds). This allows for many blocks to be produced in one working shift, and then transferred into an accelerated curing room.
Click here to view the patent on Google Patents.