Invention for Production monolithic bodies using a porous matrix by low temperature solidification in an additive manufacturing process.
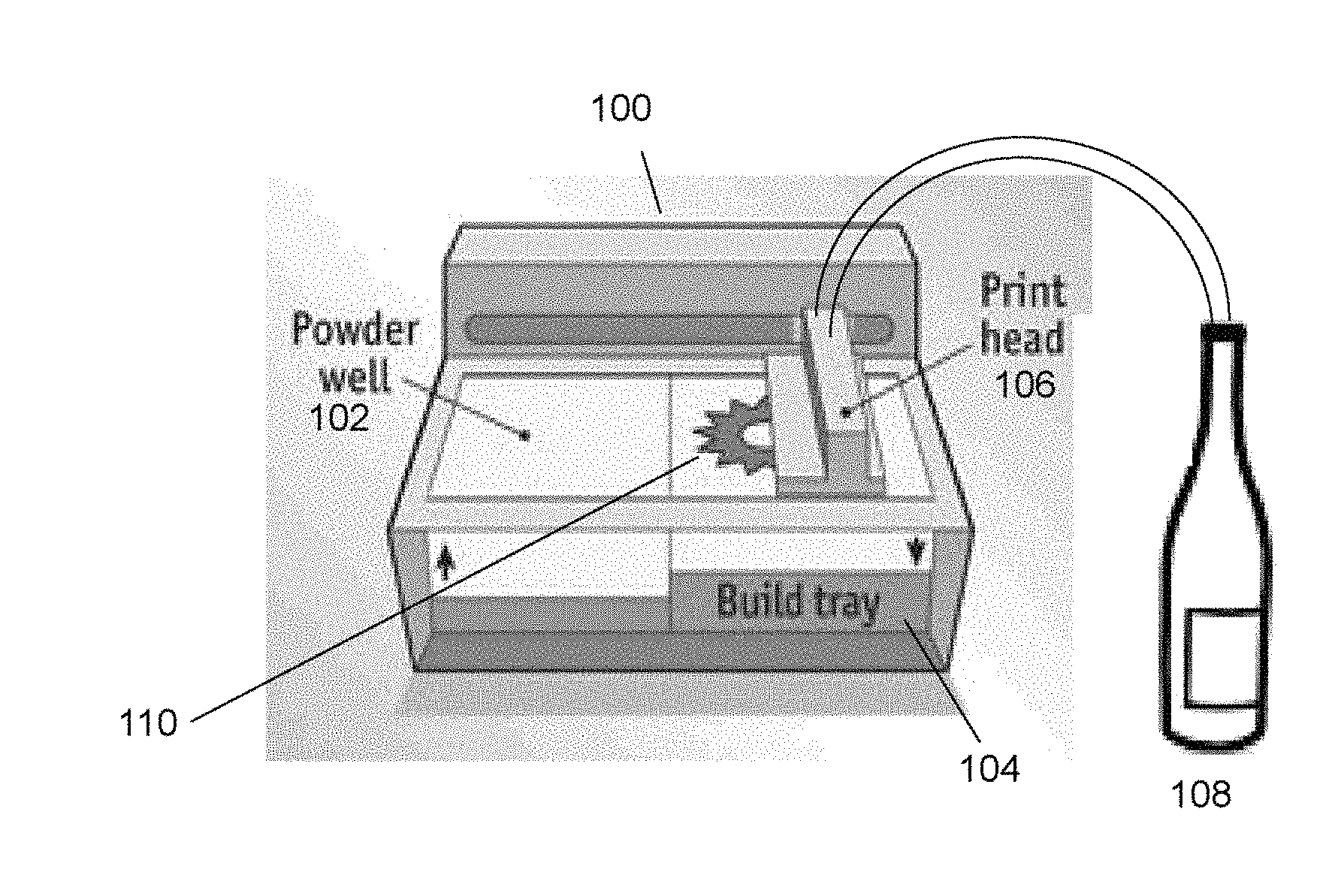
Invented by Richard E. Riman, Rutgers State University of New Jersey
Additive manufacturing, also known as 3D printing, has been around for several decades. However, recent advancements in technology have made it possible to create complex structures with a high degree of accuracy and precision. One of the most promising applications of additive manufacturing is the production of monolithic bodies using a porous matrix by low temperature solidification.
The process involves the use of a porous matrix material that is printed layer by layer using a 3D printer. The material is then solidified at a low temperature, which allows for the creation of a monolithic body with a porous structure. This structure is highly desirable in many industries, including biomedical, aerospace, and automotive.
In the biomedical industry, the porous structure of these monolithic bodies allows for the growth of cells and tissue, making them ideal for use in tissue engineering and regenerative medicine. In the aerospace industry, the porous structure can be used to reduce weight and increase fuel efficiency. In the automotive industry, the porous structure can be used to improve the performance of catalytic converters and reduce emissions.
The market for production monolithic bodies using a porous matrix by low temperature solidification in an additive manufacturing process is expected to grow significantly in the coming years. According to a report by MarketsandMarkets, the global 3D printing market is expected to reach $34.8 billion by 2024, with a compound annual growth rate of 25.76%.
The growth of this market is being driven by several factors, including the increasing demand for customized products, the need for faster and more efficient manufacturing processes, and the growing adoption of 3D printing in various industries.
In conclusion, the market for production monolithic bodies using a porous matrix by low temperature solidification in an additive manufacturing process is a rapidly growing industry with enormous potential. As the technology continues to advance, we can expect to see more innovative applications of 3D printing in various industries, leading to increased efficiency, reduced costs, and improved product performance.
The Rutgers State University of New Jersey invention works as follows
Low temperature solidification is an additive manufacturing process that produces a monolithic structure from porous materials.
Background for Production monolithic bodies using a porous matrix by low temperature solidification in an additive manufacturing process.
Additive Manufacturing (AM) is a method that uses digital 3D design data to build a component in layers through depositing material. 3D printing is one example of additive manufacturing. Other processes are described below. AM can be distinguished from traditional manufacturing methods that require material removal. A workpiece is not made from a solid block. Instead, additive manufacturing creates layers using fine powdered materials. In the different types of additive manufacturing discussed here, a variety of metals, plastics, and composite materials can be used.
An embodiment shows a method for producing a monolithic structure from a porous material, which includes low temperature solidification as an additive manufacturing process.
A further embodiment relates to a method for producing a monolithic structure from porous materials. This involves providing a layer of porous material with interstitial space and containing at minimum a first reactant. Then, the infiltrating media is allowed to penetrate at least some of the interstitial areas of the porous layer under conditions that promote a reaction of at least one reactant and at most two reactants to create at least the first product. Finally, the above steps are repeated to make a monolithic
Another embodiment describes a method for producing a monolithic structure from porous material. This involves providing successive layers of porous mat with interstitial space and at minimum a first reactant. Then, the infiltrating media is contacted the successive layers of porous mat with at least one second reactant. This allows the infiltrating media to penetrate at least some of the interstitial space of the layer of porous and allow the at most first product to form and fill the interstitial spaces.
A second embodiment describes a method for producing a monolithic structure from porous material. This involves providing a porous layer with interstitial space and at minimum a one reactant. The infiltrating media is allowed to penetrate at most a portion the interstitial areas of successive porous layers under conditions that promote the formation of at the least one product.
Monolithic bodies can be made using additive manufacturing methods like 3D printing and stereolithography. These methods are detailed in Tables 1 & 2 below. They are reprinted from Tim Hayes’,?The Future of 3D Printing? Optics & Photonics News July/August 2013, page 22 and from the Wikipedia 3D Printing webpage, Nov. 6, 2013. Some of these methods can only be used for manufacturing metals, while others are suitable for manufacturing polymers. Low temperature solidification in additive manufacturing has been shown to be capable of producing monolithic bodies from any type of material, including metals, ceramics and cermets as well as polymers or composites thereof.
TABLE 1\n3-D Printing Technologies\nTechnology Description Applicable Materials Key Players\nStereolithography Selectively cures a uniform Photopolymers 3D Systems\nlayer of material with a UV\nlaser\nDigital light Cures an inkjet-deposited Photopolymers Texas\nprocessing material layer in a support Instruments,\nmaterial with a UV light Envisiontec\nPolyjet Cures an inkjet deposited Photopolymers Objet\nlayer with multiple [Stratasys]\nmaterials using a UV light\nSelective layer Selectively fuses material Thermoplastics, EOS, Morris\nsintering powder using a laser metals Technologies\n[GE Aviation],\nOptomec\nElectron beam Selectively fuses material Metals Arcam\nmelting powder using an electron\nbeam\nSelective heat Selectively fuses material Thermoplastics Blueprinter\nsintering powder using a thermal\nhead\nFused filament Extrudes a material Thermoplastics, food, Stratasys,\nfabrication filament through wood and ceramic Makerbot,\na heated nozzle composites with a Printrbot\nthermoplastic binder\nPowder bed Selectively inkjet prints a Thermoplastics, food, Zcorp [3D\ninkjet printing liquid binder to fix material wood and ceramic Systems],\npowder into a solid composites with a ExOne\nthermoplastic binder\nLaminated object Trims sheets of material Paper, polymer films, Mcor, TNO,\nmanufacturing and joins with adhesive metal sheets Solido, Kira
TABLE 2nType Technologies MaterialsnExtrusion fused-deposition Thermoplastics PLA, ABS), HDPE, eutectic metals,\nmodeling (FDM) edible materials, Rubber (Sugru), Modelling clay, Plasticine,\nRTV silicone, Porcelain, Metal clay (including Precious Metal\nClay)\nWire Electron-Beam Freeform Almost any metal alloy\nFabrication (EBF3)\nGranular Direct metal laser Almost any metal alloy\nsintering (DMLS)\nElectron-beam melting Titanium alloys\n(EBM)\nSelective laser melting Titanium alloys, Cobalt Chrome alloys, Stainless Steel,\n(SLM) Aluminium\nSelective heat sintering Thermoplastic powder\n(SHS) [17]\nSelective laser sintering Thermoplastics, metal powders, ceramic powders\n(SLS)\nPowder-bed and Plaster-based 3D Plaster\ninkjet-head 3D printing (PP)\nprinting\nLaminated Laminated-object Paper, metal foil, plastic film\nmanufacturing (LOM)\nLight polymerised Stereolithography (SLA) photopolymer\nDigital-Light Processing photopolymer\n(DLP)
Porous matrix that contains a first reactant (i.e., a low temperature solidification) is used in the hydrothermal liquidphase densification process. A material that is capable of undergoing chemical reactions) is in contact with an infiltrating media which contains a second reactant. The product is formed when the first and second reactants react. The porous matrix containing first reactant in an embodiment is a powder. To agglomerate the powder, the porous matrix may also include a binder such as a polymer binding agent. The binder can be omitted. Another embodiment of the porous matrix contains a fluid, such as water, alcohol, or a combination thereof. Other fluids, such as non-aqueous fluids, may also be used. Any matrix or infiltrating material, including those described in U.S. Pat. No. No. 8,313,802 is attached as an attachment. It is hereby included by reference in its entirety. Low temperature solidification is used to refer to the Hydrothermal Phase Sintering method as described in U.S. Pat. No. 8,313,802.
Another embodiment involves a method for producing a monolithic structure from porous materials. This includes providing a layer of porous material with interstitial space and containing at minimum a first reactant. Contacting the porous matrix layer with an infiltrating media that carries at most a second reactant allows the infiltrating media to penetrate at least some of the interstitial areas of the porous layer under conditions that promote a reaction between at least one reactant and at least two reactant
Another embodiment of a method for producing a monolithic structure from porous material includes providing a plurality successive layers of porous mat with interstitial space and including at minimum a first reactant. Then, the infiltrating media is contacted the plurality successive layers of porous mat with at least one second reactant. This allows the infiltrating media to penetrate at least some of the interstitial space of the layer of porous mahil under conditions that promote a reaction between at the at most
A second embodiment relates to a method for producing a monolithic structure from porous material. This involves providing a porous layer with interstitial space and at minimum a one reactant. Then, the infiltrating media is contacted the porous layer with a plurality successive layers, allowing it to penetrate at most a portion the interstitial areas of successive porous layers. Finally, the infiltrating media contacts the plurality successive layers of porous mat with the infiltrating
In any of these embodiments, each layer may be contacted by the infiltrating media before supplying the next layer. Alternately, all layers of the monolithic structure may be provided first and then infiltrated with the infiltrating media. In any of these embodiments, the whole porous matrix can be infiltrated with infiltrating media. An embodiment may contain a binder material in the porous matrix. An embodiment may include a binder material that reacts with the infiltrating medium. This could result in the removal of the binder from porous matrix.
In one embodiment, heating the porous matrix layer(s) allows the at least the first product to form and fill at most a portion of its interstitial spaces. Conduction, induction and convection are all possible methods of heating the porous matrix. The porous matrix may contain a precursor for metal, a ceramic or cermet as well as a polymer or composite thereof.
An embodiment of the porous matrix is a spherical body. The porous matrix as-deposited has not been react with the infiltrating media to form the final product phase (e.g., monolithic body such as a ceramic or metal, cermet, polymer, or composite thereof).
In one embodiment, the infiltrating media may contain a gas such as CO2. The porous matrix in an embodiment is a slurry. The slurry can contain water, alcohol, or a mixture thereof such as 0-20% alcohol. An embodiment provides the layer(s), of the porous matrix (e.g. formed on a support) with the print head discussed below. An embodiment provides the infiltrating medium with a printhead, as described in greater detail below.
In an embodiment, low-temperature solidification is used in order to solidify or remove a binder from a green body during the additive manufacturing process. The green body is a powder-based ceramic, metal, or cermet material, or precursors thereof, which are deposited using a print head. Low temperature solidification is a process that involves providing a basic liquid (e.g. pH>7) to the green bodies and heating them to below 250 C to melt the binder. Another embodiment of low temperature solidification involves providing a fluid to green body and heating it to below 250 C to make the green body a monolithic solid. Low temperature solidification can be used to solidify the green body and remove the binder. This step involves providing a basic fluid to the green bodies and heating them to below 250 C to melt the binder. The green bodies then become monolithic solid bodies during this step.
An embodiment has a monolithic solid body that is smaller than the green body. Its size is within 2%. Low temperature solidification of the porous green body matrix results in virtually no shrinkage in the porous matrix layer(s). The final monolithic body will be roughly the same size as its predecessor. The shrinkage could be as low as 2% or even 1%, for example. This could be because the powder particles are not moving toward each other during low temperature solidification. Contrary to conventional high temperature sintering where powder particles in the green bodies move towards each other, shrinkage is generated. Materials that cannot withstand high temperature sintering and high temperature additive manufacturing can be made using low temperature solidification in combination with additive manufacturing.
Another embodiment of the infiltrating liquid includes a gas with a liquid in partially infiltrated high temperature solidification, or a fluid with a liquid that is fully infiltrated at low temperatures solidification. Products made using any of the above methods are also included in Embodiment.
FIG. “FIG. The apparatus 100 is equipped with a powder well/reservoir 101 in which the powder material for making the porous matrix can be stored. The apparatus 100 includes a print tray (104), on which the monolithic bodies 110 and 106 will be made, and a printhead 106 that may be used for delivering the infiltrating media (e.g. the fluid and/or the powder). The reservoir 108 may contain the infiltrating media and is connected to the printhead 106. In one embodiment, the printhead 106 can move in the X- and Y directions, while the print tray104 can move in the Z direction. As each layer of the monolithic bodies is being deposited by the printer head 106, the tray 104 is then lowered. Alternative embodiments of the apparatus 100 allow the print head to be configured to move in the Z, X, and Y directions, while the print tray 104 is stationary. Alternativly, the printhead 106 can be kept stationary while the print tray (106) is configured to move in the Z, Y, and X directions.
Click here to view the patent on Google Patents.