Invention for Photopolymerizable Inkjet Ink, Ink Cartridge, and Printer
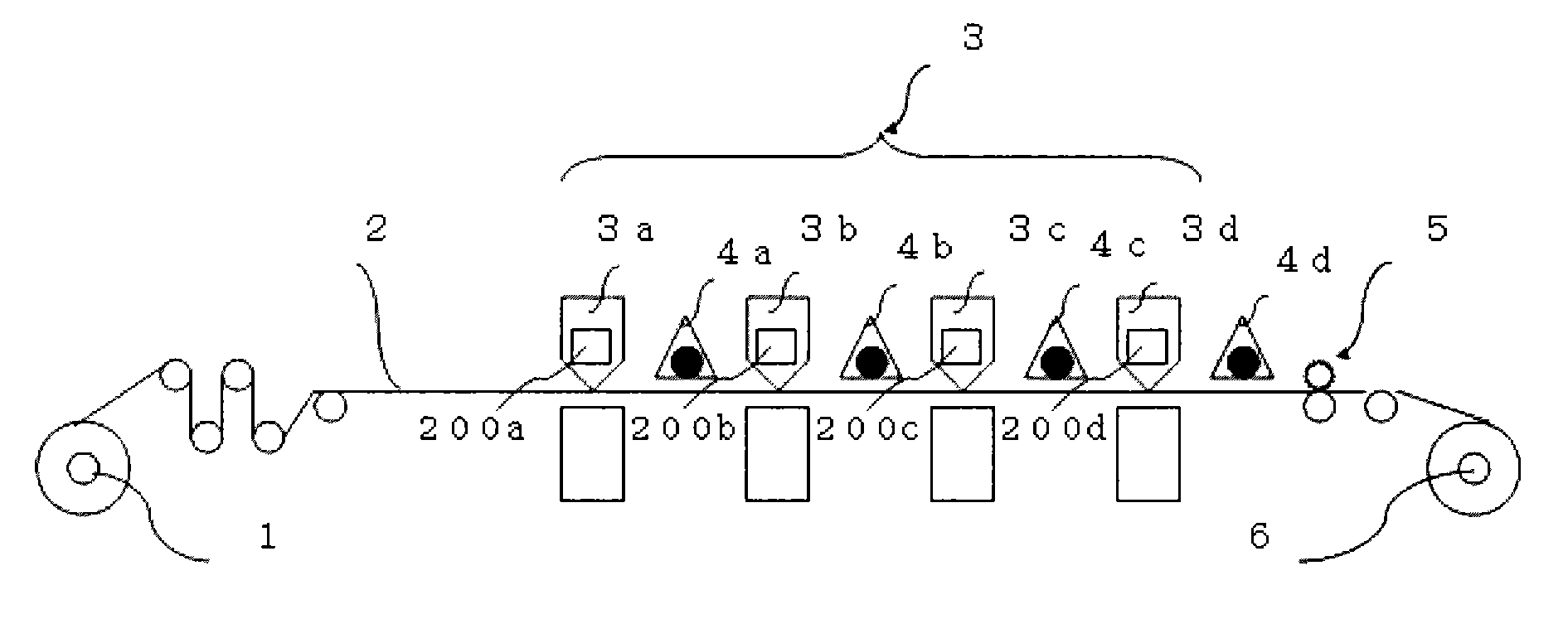
Invented by Takao Hiraoka, Ricoh Co Ltd
Photopolymerizable inkjet ink is a type of ink that solidifies when exposed to ultraviolet (UV) light. This ink offers several advantages over traditional inkjet inks, including faster drying time, improved color vibrancy, and better resistance to fading. These characteristics make it ideal for applications that require high print quality and durability.
The ink cartridge is an essential component of inkjet printers. It holds the ink and delivers it to the print head for accurate and precise printing. The market for ink cartridges has been driven by the increasing adoption of inkjet printers in both residential and commercial settings. The demand for ink cartridges is expected to grow further as more businesses and individuals switch from laser printers to inkjet printers due to their lower cost and improved print quality.
The printer itself is another crucial component of the market. Inkjet printers that are compatible with photopolymerizable inkjet ink have gained popularity due to their ability to produce high-resolution prints with vibrant colors. These printers are widely used in industries such as graphic design, photography, and textile printing. The market for photopolymerizable inkjet printers is expected to grow as more businesses invest in advanced printing technologies to meet the increasing demand for high-quality prints.
One of the key drivers of the market for photopolymerizable inkjet ink, ink cartridge, and printer is the growing e-commerce industry. With the rise of online shopping, there is an increasing need for high-quality product packaging and labeling. Photopolymerizable inkjet ink offers excellent print quality and durability, making it an ideal choice for printing product labels, barcodes, and packaging designs. This has led to a surge in demand for ink cartridges and printers that are compatible with this type of ink.
Additionally, the textile industry has also contributed to the growth of this market. Photopolymerizable inkjet ink is widely used in textile printing for creating vibrant and long-lasting designs on fabrics. The ability of this ink to adhere well to various types of textiles and withstand multiple washes has made it a preferred choice for textile manufacturers. As the demand for customized and digitally printed textiles continues to rise, the market for photopolymerizable inkjet ink, ink cartridge, and printer is expected to grow further.
In conclusion, the market for photopolymerizable inkjet ink, ink cartridge, and printer has witnessed significant growth due to the increasing demand for high-quality prints in various industries. The advantages offered by photopolymerizable inkjet ink, such as faster drying time and improved color vibrancy, have made it a preferred choice for businesses and individuals alike. As the e-commerce industry and textile printing sector continue to expand, the market for these products is expected to grow further in the coming years.
The Ricoh Co Ltd invention works as follows
The inkjet photopolymerization ink includes: a monomer with a Stimulation Index of less than 3; the Stimulation Index is a measure of the degree of skin sensitization, as determined by the Local Lymph Node Assay. It also contains a phenolic aromatic compound that has two hydroxyl groups within the molecule.
Background for Photopolymerizable Inkjet Ink, Ink Cartridge, and Printer
Photopolymerizable Monomers are used in photopolymerizable Inkjet Inks. Examples include (meth-)acrylic ester compounds, acrylic amide compounds and cation polymerizable Oxetane Compounds. The (meth-)acrylic ester compounds and the acrylamide compounds are preferred because they are readily available, cheap, easy to procure, and can be used with a radical photopolymerization catalyst that is commonly used and inexpensive.
The compounds of (meth-)acrylic ester and acrylamide are toxic. While some are mild in terms of skin irritation and oral toxicity, inkjet inks with low viscosity are not safe in terms of skin sensitization.
The present inventor has conducted extensive research and found that some materials are safe for skin sensitization. The present inventor found, through further research, that some (methacrylic) acid ester and acryl amide monomers were suitable for photopolymerization and had a Stimulation Index value (SI) less than 3. This Stimulation Index is based on a skin-sensitization test based upon the LLNA. When these compounds are formulated to achieve a curing ability that is practically useful, their curing properties become inferior to the commonly used photopolymerizable Inkjet inks. A photoradical polymerization initiater has to be added in greater quantities than usual. The inks produced by this process were not stable enough to be stored in environments with high temperatures, such as the summer.
The present inventor also found an inkjet photopolymerization ink that is not skin-sensitizing, which improves the coating film’s curing properties, allows curing failures to be confirmed visually, and simplifies quality control during the production process. The photopolymerizable Inkjet Ink contains a number of monomers that are photopolymerizable and have a SI less than 3. It also contains a self-cleaving initiator of polymerization, a hydrogen-abstracting initiator of polymerization, and an amine as a polymerization accelerater. Even this photopolymerizable Inkjet Ink has a difficult time achieving the storage stability described above.
As is well known, a polymerization inhibitor can improve the storage stability of photopolymerizable Inkjet ink. Polymerization inhibitors can include quinones such as benzoquinone or methoquinone as well as aromatic secondary amines such as diphenylamine and phenothiazine.
However even with the addition of a polymerization inhibitor such as methoquinone to the newly discovered compound, the inks will still thicken or solidify due to polymerization.” It was also found that secondary amines such as phenothiazine, which have a high polymerization inhibitory effect, cannot be used because of their colorant properties.
Furthermore many photopolymerizable Monomers with a SI Value of less than three have high viscosity in inkjet inks. The addition of a Polymerization Initiator increases the viscosity of the inks. It is therefore important to take the proper steps to reduce ink viscosity. It is possible to reduce the viscosity of inks by adding a diluent. The diluent is not recommended because it will volatize and be released into the air, causing adverse effects on the environment. Inks shouldn’t contain solvents. Inks that contain water-soluble monomers can be reduced in viscosity by adding water. When non-permeable materials, such as plastics, are used, the water penetration into these materials may not be possible. In order to achieve a high-speed print process, it’s necessary to instantly volatize the water for drying. To do this, in many cases a heat source is required, which is not the most energy-efficient option.
CITATION LIST
Patent Literature
PTL 1 : Japanese Patent Application Laid Open (JP A) No. 04-164975″ 04-164975
PTL 2: JP-A No. 2005-290035
Technical Problem
The present invention aims to develop a photopolymerizable Inkjet Ink that has good storage stability and is not skin-sensitizing.
Solution to Problem
The following are the means for solving these problems. “Specifically, a polymerizable inkjet of the present invention contains a monomer photopolymer with a Stimulation Index of less than 3 where the Stimulation Index indicates an extent of skin sensitization measured by a Skin Sensitization Test (LLNA); as well as a phenol-aromatic compound that has two hydroxyl groups within the molecule.
The Advantageous Effects of Invention
The present invention provides a photopolymerizable Inkjet Ink that is non-sensitizing to the skin and has good storage stability at higher temperatures.
BRIEF DESCRIPTION DES DRAWINGS
FIG. “FIG.
FIG. “FIG.
FIG. “FIG.
Click here to view the patent on Google Patents.